If you use Sage 500’s O2 Process Manufacturing module, then you know RKL acquired O2 from EVS in early 2020. With a smooth transition completed, RKL is happy to be supporting customers and making minor modifications for ad-hoc requests. What you may not know, is that RKL has also been working on an 8.00.3 minor revision to support Sage 500 8.00.3 and potentially further minor updates, and we have included several fixes and enhancements that you may find useful in your everyday operations. I’ll go through a high level overview of those changes in this blog. The source version of issues is not mentioned, as we did not investigate each issue for the originating release.
As with the release, this blog was put together with the help of many team members.
Production Close Not Validating Labor and Clearing Transaction Dates
The start and end dates of Labor and Clearing transactions dates are assign from the batch close process, but the dates are not validated against closed periods. This error makes the rest of the batch inaccessible via the screens
Material Returns Leaving Pending Inventory Transactions
In some instances, a work order return of a material issue would not remove a pending inventory transaction. There would then be both a posted and a pending transaction for the return, resulting in double counting the inventory.
Production Entry Allows Return of Full Amount Available, Not Just Production Amount
If you produce the same lot and amount in two batches and put it in the same bin, one of the production entries will allow you to return the full amount – the sum of the two production entries – which it shouldn’t, since the other might be returned as well. It should limit its return the amount it produced
Finished Goods Estimated Cost including non-financial cost codes in calculations when entering production batches
When entering production batches, the issue was present in the Estimated Cost portion in the selection of the cost code values; because it wasn't restricting by GL Account type it would also include non-financial accounts. However, the account type restriction was happening properly in the Actual Cost section. Not restricting the GL account type in the estimate caused three issues: First, some of the production batches GL Transactions weren't processing to GL, since the GL Integration excludes non-financial accounts. Second, AR Invoicing won't post because the item has costs in a non-financial account for COGS, which will cause invoice posting to error. Third, this caused differences in labor costs between actuals and estimates and caused it to update cost buckets that aren't used normally.
Bill of Material (BOM) line duplication in Critical Material Inquiry.
The material requirement for each BOM line will be duplicated by the number of BOMs in which it exists. This issue is just a duplication of display.
Item BOM Report Showing duplicate/un-needed BOM Lines.
In multilevel production, if a Finished Good (FG) BOM item is being used in another formula at a lower level, the report was including that material in the BOM explosion on the Item BOM report and in costing. This was true even if these higher-level FG BOM items did not have a default formula specified. The report should not display any BOM items that don't have a default formula.
O2 Item Bin view ignores 'Use Distribution Preferred Bins as Manufacturing Bins" setting
If a company is setup for O2 Process Manufacturing (PM) and doesn't specify specific manufacturing bins, but instead denotes distribution preferred bins as their manufacturing bins via the checkbox, this view will not return any bins in the selection list when entering production transactions. When using the O2 Production Entry screen, when you enter a production line the bin number should default from the preferred bin (based on the spo2PNGetFGDist stored procedure). This procedure gets the default bin using the vo2ItemBin view. This view assumed that advanced production is enabled and manufacturing bins are separately maintained. If instead, distribution bins is used as the manufacturing bin then no bin is found and returned.
QC Sample Sub Classes returning the wrong test details to add to battery in multi-company environments
In a multi-company environment, it is possible that a sample in one company and the sub-class of another sample in a different company will have the same surrogate key. This could result in getting the wrong test details to add to battery. This happened because it was using the class information to lookup subclass information, when no subclass information existed for that QC sample class. The solution was to only get subclass information if it exists.
zO2 Formula Delete Material Error
If you tried to delete a line in this .Net based screen, you would receive an error message. The ability to save a line also would sometimes produce an error as well. These both have been remedied.
zO2 Critical Material Inquiry – Cosmetic Issues
We corrected several display issues with this form, including blank fields displaying cryptic code scripting fields, field labels obscuring the actual fields, such as the Period Summary Start Date and Cut-off Date labels, and partially hidden field names. These were just display issues, but when you can’t read data, that’s not a nice screen. A couple examples of the cosmetic fixes are shown below.
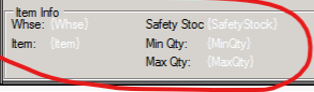
Figure 1- Item Info before Fix
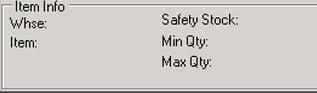
Figure 2 - Item Info after Fix
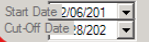
Figure 3 - Start Date & Cut-Off Date before Fix
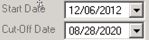
Figure 4 - Start Date & Cut-Off Date after Fix
Arithmetic Overflow
Some screen processes may result in arithmetic overflow if using small units of measure and large quantities. This has been seen in O2 Issue Material Finalization for example and Receipt of Goods posting
Sort order on Production BOMs is not the same as the defined BOM lines
If a BOM is created with a given set of lines, and a Production batch is then created for that item/BOM, the order of lines in the production batch is not the same as in the BOM definition. A re-ordering of the BOM lines is occurring when the PN BOM Line Keys are being generated, causing the sequence to not match the intended sort order.
MRP improperly calculating remaining demand adjustment for periods with more than one sales order or shipment
When using demand adjustment, the value is supposed to net with the same-period sales orders and shipments to calculate a "remaining" demand adjustment to be used in the MRP run. We found that only the first matching period sales order and first matching period shipment were being considered leading to wrong replenishment guidelines.
This can occur, for example if an item/warehouse has a demand adjustment per period and at least two sales orders and at least two shipments exist for that inventory for that period. Running MRP for that timeframe, you will notice that the demand adjustment quantity is not properly calculating.
Critical Material Inquiry Not Forecasting Demand Properly
When using projected demand or future demand adjustment, if there were sales orders or shipments scheduled for the same period that exceeded the demand adjustment amount, the Sales order/Shipment Quantity would be added twice against the demand adjustment amount resulting in an incorrect Projected Demand in zO2 Critical Materials Inquiry.
Item BOM Cost Roll Up Report
The form is not allowing the selection of the options for rolling up the formulas for an item. It will either use the Default Formula or Formula by Warehouse based on a company-level setting. This was changed to allow the flexibility of either in the report
Expand MRP Purchase Items from One Choice to Two
Just as Sage has done in the Sage 500 MRP Screen, the O2 MRP screen now also has the two check box choices for replenished purchase items and manually purchased items.
In Summary
We hope that from the list above and any interactions you’ve had with the RKL team during these initial months that you’ve been our customers for O2 have shown you our commitment to you and to making O2 fit your business, enabling you to innovate and to complete your daily tasks with ease and efficiency.